Everidge Gains Better Visibility & Inventory Control with Move from Dynamics GP to Dynamics AX
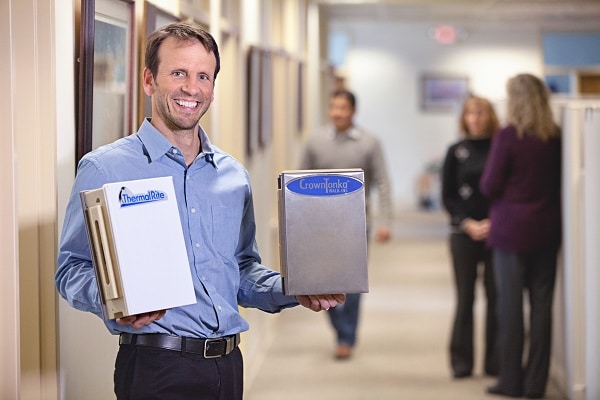
Everidge Gains Better Visibility & Inventory Control with Move from Dynamics GP to Dynamics AX
With more than 50 years of experience in the cold-storage industry, Everidge is made up of three brands including Crown Tonka, ThermalRite and ICS. Based in Plymouth, Minn., Everidge is known for their dedication to product quality and superior customer service.
They manufacture indoor and outdoor walk-in cold storage and distribute specialty refrigeration equipment and replacement parts. They have seven locations (four manufacturing sites) throughout the United States and distribute their products globally.
Moving to Dynamics AX
In the competitive manufacturing and distribution industry, profit margin is directly impacted by costs.
When CFO Mike Polis joined Everidge eight years ago, his first order of business was to gain control of costs. “In order to better control our costs, we had to have better visibility of our inventory,” he said.
At that time, Everidge was using Microsoft Dynamics GP, which has limitations with multisite inventory control and language support. Polis began looking at alternatives to replace Dynamics GP and after senior management reviewed options, they decided Microsoft Dynamics AX would better suit the company’s needs. Dynamics AX was designed to support multi-site manufacturers where materials are shared across multiple facilities.
Polis says the transition from Dynamics GP to AX went well. He identified four key components of the transition plan that led to a successful implementation:
- Identify project resources and accountabilities
- Engage sponsors to support the project
- Ensure internal users dedicate sufficient time to the project
- Appoint a resource to drive user adoption
Partnering for Success
In addition to driving the selection of Dynamics AX, Polis also sought a new Dynamics AX partner to ensure Everidge would achieve the highest return on their Dynamics investment by moving to Dynamics AX 2012.
When he heard that Stoneridge Software had recently launched a new partner organization with a focus on local customers, he knew it would be a good fit for his needs. “What caught my eye about Stoneridge Software was their product knowledge,” Polis said. “I love the fact that they have true product experts.”
As a standard practice, Everidge avoids customizations and the flexibility inherent to Dynamics AX has enabled the company to use much of its standard functionality. “Stoneridge Software provided guidance and options that enabled us to adapt our business processes to Dynamics AX versus adapting AX to our existing processes,” said Polis.
While they avoid customizations when possible, they have made several modifications to accommodate needs unique to their business model.
“There’s an art to presenting a modification. I appreciate that Stoneridge Software’s development staff understands the practical application of ideas as we’re developing a modification,” Polis said. An additional benefit of Dynamics AX is the flexibility to embed and manage customizations more effectively.
Inventory Control
One of the driving factors in transitioning to Dynamics AX was better inventory control and Dynamics AX has delivered. “Dynamics AX has proven to be a very effective solution for our inventory control. We now have greater visibility into each of our sites,” said Polis.
Dynamics AX offers multiple levels of inventory tracking (site, warehouse, aisle, location, and pallet), whereas their previous solution, Dynamics GP only incudes bin and site.
Polis said the inventory and product dimensions in AX 2012 have been very beneficial. Using inventory dimensions ensures dimension values are included on all inventory transactions, which enables users to easily track the location of inventory items.
Using product dimensions has also benefited Everidge by providing a more detailed inventory view. Product dimensions identify product variants, which allows Crown Tonka to create aggregate inventory reports to better control their inventory across sites.
In addition to inventory control, product dimensions have allowed Everidge to reduce their Stock Keeping Unit (SKU) count. “In Dynamics AX I can have one SKU with endless configurations,” Polis said.
Everidge will continue to capitalize on the efficiency improvements they’ve realized since moving to Dynamics AX 2012 and partnering with Stoneridge Software.
“I’m really happy with our decision to move to Dynamics AX 2012 and partner with Stoneridge Software,” said Polis. “The product is flexible and scalable and works well for our industry and Stoneridge Software is a true partner. When we need attention, we get it and I know what we need to be done will be done right.”
Benefits:
- Sound architecture and flexibility of the software allowed use of standard AX functionality
- A more detailed inventory view with multiple levels of inventory tracking such as site, warehouse, aisle, location, and pallet
- Addition of product dimensions which identified product variants made for a reduction of SKU counts
- Creation of aggregate inventory reports to better control inventory across sites
- Platform ensures agility and scalability as business grows and changes